Chemistry of Christmas Ornaments
How Christmas ornaments are made
Often, it doesn’t occur to us to wonder where simple things come from, and Christmas ornaments are no exception. The process of making fragile Christmas decorations involves a whole manufacturing story: the gradual transformation of a piece of glass into a tiny masterpiece.
The process starts with cutting the glass, which is delivered to a factory in the form of long, thin tubes. Such a tube is cut into smaller sections known as blanks. The glass is then heated to about 1000 °С (1832 °F), and it becomes soft and ductile — somewhat similar to dough.
Glass is an amorphous substance, meaning that it doesn’t have a regular crystalline structure. That’s why, upon heating, glass becomes less dense, which makes it easier to mold.
Next, a glass-blower shapes the blanks. Christmas ornaments with a relatively simple shape, such as balls and cones, are made by solely the glass-blower, who exhales air into the glass blanks.
More complicated shapes are produced using compression molds. After the glass blank is heated, a glass-blower puts it into a mold and exhales air with all his or her might.
Curiously, during this manufacturing process, the glass is thinned to a fraction of a millimeter, becoming as fragile as an eggshell.
Because of its amorphous structure, glass is not very thermally conductive. A glass blank doesn’t burn a master’s mouth and hands, even when its other side is heated to 700 °С (1292 °F)! Still, more complex Christmas ornaments are made in compression molds. This includes shapes such as Santa Claus, snowmen, various cars, stars, and so on.
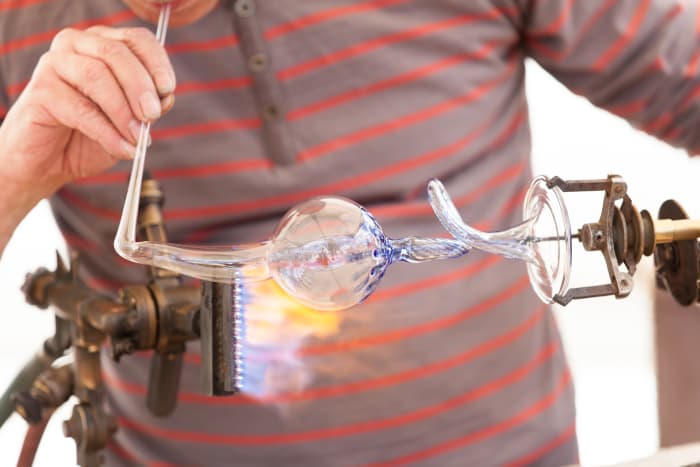
Next, an ornament must be cooled. To ensure that it cools evenly, the ornament is held to a burner flame, and then the flame’s temperature is gradually lowered.
Once the ornament is cooled, it undergoes a silvering process.
The silvering process takes place inside an ornament. First, a silver plating solution is poured into the figure. This is usually a solution containing silver ions and a reducing agent, such as potassium sodium tartrate tetrahydrate and glucose.
Another technique involves aluminum deposition. Ornaments are placed in a special vacuum chamber and aluminum foil is hung on a tungsten wire. Next, electrical current is passed through the tungsten wire, causing the aluminum to evaporate and precipitate on the surface of the ornaments.
During the silvering process, a glass blank is immersed in water heated to about 50 °С (122 °F), where it is steadily shaken to promote a chemical reaction. Silver ions interact with molecules of a reducing agent, causing the silver to cover the glass surface in a thin, glossy layer.
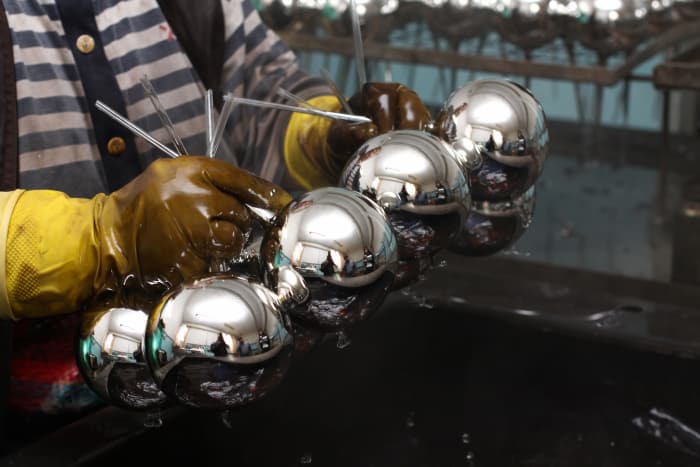
The leftover solution is disposed of and subjected to a corresponding treatment. The ornament product is washed and sent onward to the next step.
Adding a finishing touch of paint can make an ornament truly festive. In order to “paint” the silver coating certain “colors”, an ornament is immersed in a colored finish. Its color and composition may vary — for instance, it may include resin, a solvent, and an aniline dye.
A mirror-like coating inside the ornament can be seen through its walls. Any excess of polish is removed, after which the ornament is dried and continues on to a painter for additional handmade decoration or is prepared for delivery straight to stores.
The last step is shaving. A blank “leg” is pre-cut and capped with metal and a loop, and the ornament is packed for sale. This fragile beauty is finally ready to decorate your Christmas tree!
Today, glass Christmas ornaments are gradually being replaced by plastic alternatives that are cheaper both in raw materials and in production costs.
However, we can find factories that produce Christmas ornaments using the good methods of old. Such factories still exist in Germany, Poland, and Russia.