Features of the dehydrogenation process of butane
How dehydrogenation reaction of butane takes place
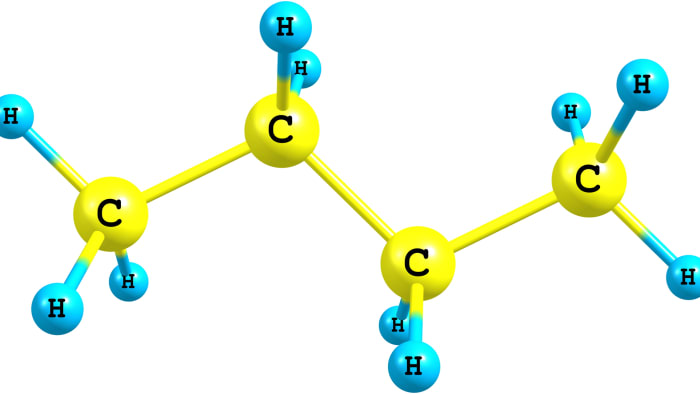
The dehydrogenation reaction is the reaction of hydrogen atoms splitting off from an organic molecule. This is a catalytic process – i.e. the presence of a catalyst is required to carry it out. Different unsaturated compounds may be products of dehydrogenation: for example, alkenes and alkadienes. In the dehydrogenation of lower alkanes (with a carbon chain of a length of C₂-C₄), molecules do not form a cycle. This is characteristic for alkanes with a carbon chain containing more than 4 carbon atoms. The features of the dehydrogenation reaction of lower alkanes can be seen clearly based on the example of hydrogen splitting off from the butane molecule.
Reaction conditions
For hydrogen to split off from a saturated aliphatic (non-cyclical) hydrocarbon, heating of up to 500-600 °C (or 932-1112 °F). Various metals are used as catalysts – for example, Ni, Pt, Pd and Fe are suitable, and also the oxides ZnO, Cr₂O₃ and Fe₂O₃.
In certain conditions, an alkadiene rather than an alkene may form from butane of normal structure (CH₃-CH₂-CH₂-CH₃) during dehydrogenation. The reaction must be conducted in the presence of the catalyst Cr₂O₃/Al₂O₃ at a temperature of 450-620 °C, or 842-1118 °F.
How the dehydrogenation reaction takes place
In dehydrogenation, C-H bonds are torn, hydrogen atoms split off from neighboring carbon atoms, and in this place a double bond forms.
In the dehydrogenation of n-butane, a mixture of isomers may form (substances with an identical atomic composition and molecular mass, but with different structure or spatial position of atoms). 2 products of reaction form – butene-1 and butene-2:
2CH₃-CH₂-CH₂-CH₃ = CH₃-CH=CH-CH₃ + CH₂=CH-CH₂-CH₃ + 2Н₂
butene-2 and butene-1 form respectively, in the presence of Ni at a temperature of 500 degrees °C (932 °F)
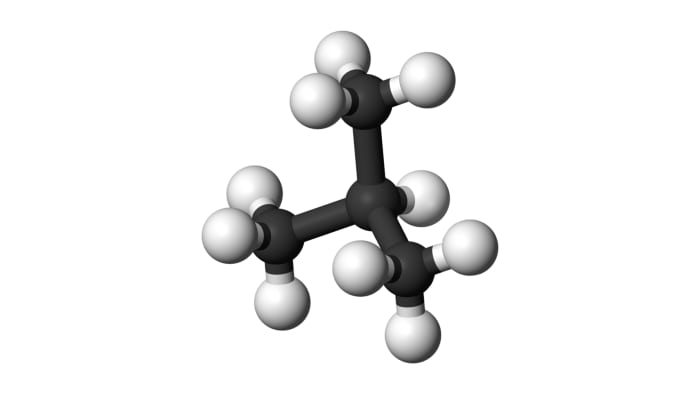
From isobutane, isobutylene may be obtained:
(CH₃)₂CH-CH₃ = (CH₃)₂C=CH₂ + H₂
reaction takes place with heating to 550-600 °C (1022-1112 °F): the chromia-alumina catalyst Cr₂O₃/Al₂O₃ is used
With the chromia-alumina catalyst, at a temperature of 450-650 °C (842-1202 °F), butadiene-1,3 forms from butane.
CH₃-CH₂-CH₂-CH₃ = CH₂=CH-CH=CH₂ + 2H₂
In dehydrogenation, butane does not form in a cycle and does not form cyclobutene because cyclobutene has an unstable structure; at the reaction temperature it is also capable of thermally breaking down to ethylene СН₂=СН₂.
Procedure for obtaining butylenes in a reactor
A reactor for obtaining butylenes from n-butane is a tubular device. In the dehydrogenation of butane, hydrocarbon goes to the device in compressed form (in normal conditions, butane is a gas which easily changes to liquid at -0.5 °C or 31.1 °F). With a piston, butane is moved to the heat exchanger, where it is heated, evaporated, and thus changes to gaseous form. Then in the tubular heater the butane is heated to the temperature required for the reaction (around 500 °C, or 932 °F).
Heated butane vapor passes into the tubular reactor (a heated catalyst is contained in the pipes). On making contact with the catalyst, the butane vapor dehydrates, forming a mixture from unreacted n-butane, butylenes (butene-1 and butene-2), hydrogen and secondary products. The mixture cools, and then breaks down. The catalyst should not make contact with the butylene for more than 2-3 seconds, otherwise a large quantity of secondary products and soot may form, which affects the yield of the product of reaction – butylene.
Click here for amazing chemistry experiments with detailed descriptions.
Process for obtaining butadiene in a reactor
After the separation of secondary products, butane and butylene in the mixture, butylene may be subjected to further dehydrogenation – in this way butadiene-1,3 can be obtained.
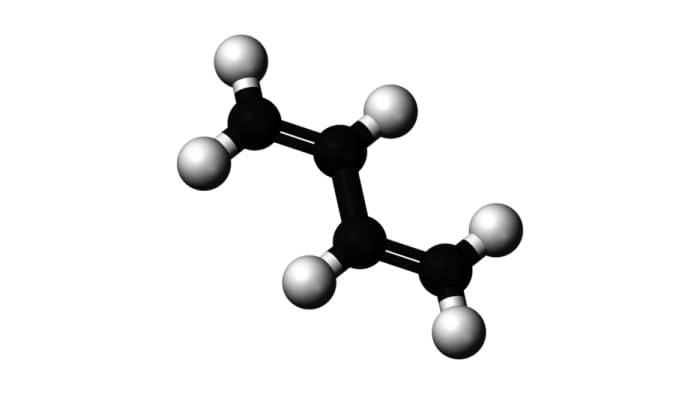
On the whole this process is technologically similar to the process used in the dehydrogenation of butane, but includes a number of special features:
- the formation of divinyl (butadiene-1,3) is also possible without a catalyst (only with heating), but the yield of the product does not exceed 40%, while when catalysts are used the yield is around 77%;
- the yield of butadiene-1,3 can be increased by decreasing its partial pressure in the reactor – this can be achieved by adding water vapor to the butylene vapor;
- after dehydrogenation, the reactive mixture must be swiftly cooled (“chilled”) in a special plate column in the device, as at a high temperature butadiene may break down.
Divinyl (butadiene-1,3) can be obtained in one stage directly from butane (a mixture of pure butane with the unreacted butane-butylene mixture must be put into the reactor), but the yield of the product will be lower than in the dehydrogenation of butane in two stages.
Catalytic dehydrogenation of butane is used in industry for obtaining unsaturated hydrocarbons. The reaction is often carried out in practice, as it takes place with high product yields – up to 80-90%.